Hafnium carbide - now that's hot!
- davidrooke
- Jun 26, 2019
- 2 min read
Updated: Nov 25, 2020
CVD is a highly flexible process that can be used on a wide range of compounds offering coatings with exceptional physical properties. But there is still a great deal of new R&D that can be done to create new breakthrough coatings.
Hafnium carbide is the most refractory binary compound known to man with a melting point of 3890degC. 480 degrees higher than tungsten! The mixed carbide tantalum hafnium carbide has an even higher melting point of 3942degC. Considering the surface of the sun is ‘only’ 5500degC or so, that’s pretty mind-blowing!
Just like its better known fellow Group4a elements, titanium and zirconium, it can (of course) be deposited by CVD by the reaction of hafnium tetrachloride with methane in the presence of hydrogen.
As a CVD coating HfC, just like its close relative, titanium carbide, TiC, is used on cutting tools, but more interestingly it is also used as a barrier layer to protect the fibres in carbon fibre reinforced carbon composites (CFCs) from oxidation at high temperatures. At first sight this seems pretty odd because HfC by itself has a poor oxidation resistance, but in combination with a carbon underlayer and a silicon carbide over-layer (both also deposited by CVD) a great protective thin film of mixed oxides is formed.
As far as we know nobody has tried to deposit Ta4HfC5 by CVD. Would it help solve your coating challenge?
We would love to discuss your particular coating challenge. We can bring to bear 100 years of experience of CVD and related coating processes across the whole “periodic table” working on some of the most challenging coating engineering problems to assist in developing a R&D programme or system to meet your challenge.
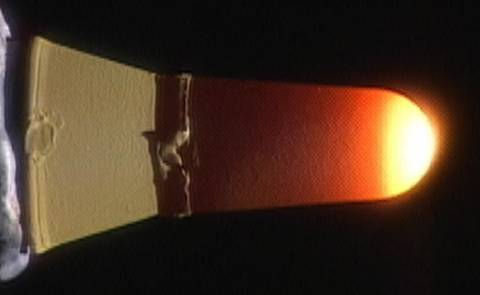
Comments